TWI (Training Within Industry) is a dynamic program, originally developed to bolster the manufacturing workforce during World War II. It has since evolved, intertwining with the digital age, and shaping the future of workforce training and operational excellence. In this comprehensive exploration, we delve into the essence of TWI, its historical significance, methodologies, and its transformative journey into the digital era, highlighting advanced software solutions that enhance and streamline the creation of work instructions in alignment with TWI principles.
Table of Contents
ToggleUnderstanding TWI: Training Within Industry
Training Within Industry (TWI) is a structured approach to workplace training, focusing on enhancing job instruction, job methods, and job relations. It’s a methodology designed to empower supervisors and team leaders to effectively instruct their workforce, improve work processes, and resolve conflicts, fostering a productive and harmonious workplace environment.
The Genesis of TWI
TWI emerged during the tumultuous times of World War II. Faced with an acute shortage of skilled labor and the pressing need to ramp up industrial production, the United States embarked on this initiative to swiftly and efficiently train new workers in various industries. The program’s success was monumental, significantly contributing to the Allied forces’ industrial might during the war.
Impact of TWI During World War II
During World War II, TWI dramatically reshaped the industrial landscape. It enabled industries to quickly adapt to the changing workforce, which included a significant influx of unskilled labor and women entering the workforce for the first time. TWI’s structured training programs ensured that quality and productivity did not suffer despite these rapid changes.
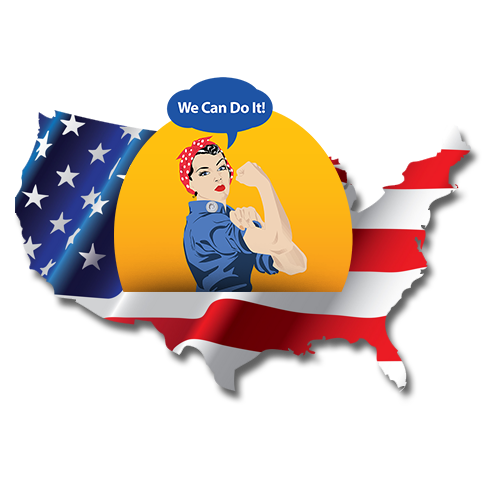
TWI Program in the US
Swift Training for the Growing Workforce
With the outbreak of World War II, the US Army faced an immediate need to massively expand its workforce. This expansion included not only soldiers on the front lines but also a substantial increase in support personnel for various logistical, technical, and administrative functions. Training Within Industry facilitated the rapid assimilation of new recruits and civilian workers into military roles, drastically reducing the learning curve and time typically required for training.
Inclusion and Utilization of Diverse Workforce Segments
The war effort led to an unprecedented inclusion of diverse segments of the population into the workforce, including women and minorities, who were not traditionally part of the industrial or military workforce. TWI’s structured and standardized approach to training proved instrumental in effectively integrating these new workforce segments, ensuring that every individual, irrespective of their background, could contribute effectively to the war effort.
The Methods of TWI
TWI comprises three core training programs, each addressing crucial aspects of workplace efficiency and harmony.
Job Instruction (JI)
This method focuses on training individuals to quickly and correctly perform their assigned tasks. It involves breaking down jobs into manageable steps, delivering clear instructions or SOP, and ensuring that the worker understands and can execute each step proficiently.
Job Methods (JM)
Job Methods training aims at improving the way jobs are done. It encourages workers and supervisors to collaborate in analyzing current methods and devising more efficient ways to use people, machines, and materials.
Job Relations (JR)
This aspect of TWI focuses on building positive employee relations, resolving conflicts effectively, and promoting a cooperative work environment. It emphasizes understanding human relations and handling problems in ways that boost morale and productivity.
TWI in the Digital Era
With the advent of digitalization, TWI is undergoing a transformative evolution. Digital technologies offer new platforms and tools for implementing TWI principles more effectively and at scale.
The Evolution of TWI with Technology
In the digital age, TWI’s principles are being integrated with cutting-edge technologies like virtual reality (VR), augmented reality (AR), and advanced software solutions. These tools not only enhance the training experience but also enable continuous improvement in job instructions and methods.
Software for Creating Work Instructions
Modern software solutions have revolutionized the way work instructions are created, maintained, and distributed. These digital platforms enable the seamless integration of TWI’s Job Instruction method, ensuring that work instructions are clear, accessible, and easily updatable.
The Future of TWI and Digitalization
As we look to the future, the synergy between TWI and digital technologies promises a new era of workplace efficiency and training excellence. From AI-driven analytics for continuous improvement to VR-based training modules, the innovation potential is boundless.
Conclusion
Training Within Industry (TWI) has come a long way from its origins in the 1940s. Its core principles remain as relevant today as they were during World War II, adapting and evolving with the digital age. The future of TWI lies in its ability to integrate with digital technologies, creating a more efficient, skilled, and harmonious workforce. As we embrace the digital future, TWI stands as a testament to the enduring power of structured training and continuous improvement.
In the realm of digital transformation, TWI continues to be a pivotal force, guiding industries toward operational excellence and setting the stage for a future where technology and human skill harmoniously coexist. As we navigate this digital era, the principles of TWI, coupled with advanced technological solutions, are set to redefine the standards of workforce training and productivity.