TPM – Total Productive Maintenance – represents a holistic approach to equipment maintenance, aimed at achieving perfect production with no breakdowns, no small stops or slow running, no defects, and no accidents. TPM emphasizes the importance of empowering all employees, from the shop floor to the top management, to participate in maintenance processes. Originating in Japan in the 1970s, TPM has become a foundational element in the pursuit of manufacturing excellence across the globe. It seeks to maximize the effectiveness of production equipment, improve product quality, and ensure a safe working environment, thereby contributing to the overall operational efficiency and profitability of an organization.
Table of Contents
ToggleThe Core Objectives of TPM
TPM is built around eight key pillars, each focusing on different aspects of maintenance and production:
- Autonomous Maintenance: Encouraging operators to take responsibility for their equipment’s routine maintenance and minor repairs.
- Planned Maintenance: Develop a scheduled maintenance program to prevent breakdowns and ensure equipment operates at its optimal capacity.
- Quality Maintenance: Aiming to eliminate product defects by managing equipment with precision, thereby ensuring quality is built into the production process.
- Focused Improvement (Kaizen): Continuous efforts to improve production efficiency and equipment effectiveness.
- Early Equipment Management: Involvement in the design and installation stages of equipment to ensure reliable and maintainable equipment from the start.
- Training and Education: Providing employees with the skills and knowledge required to effectively participate in TPM activities.
- Safety, Health, and Environment: Ensuring a safe and healthy working environment while minimizing environmental impact.
- TPM in Administration: Applying TPM principles to administrative and support functions within the organization.
The Role of Standardization in TPM
Standardization is a critical aspect of successfully implementing TPM. It involves creating clear, concise, and comprehensive standard operating procedures (SOPs) for all maintenance and production tasks. These SOPs serve as a foundation for training, a benchmark for performance, and a basis for continuous improvement. By standardizing TPM activities, organizations can ensure consistency in how tasks are performed, reduce variability, improve efficiency, and enhance safety. Standardization also facilitates easier knowledge transfer, allowing employees to learn from best practices and avoid reinventing the wheel.
See the Ranking for SOP Software
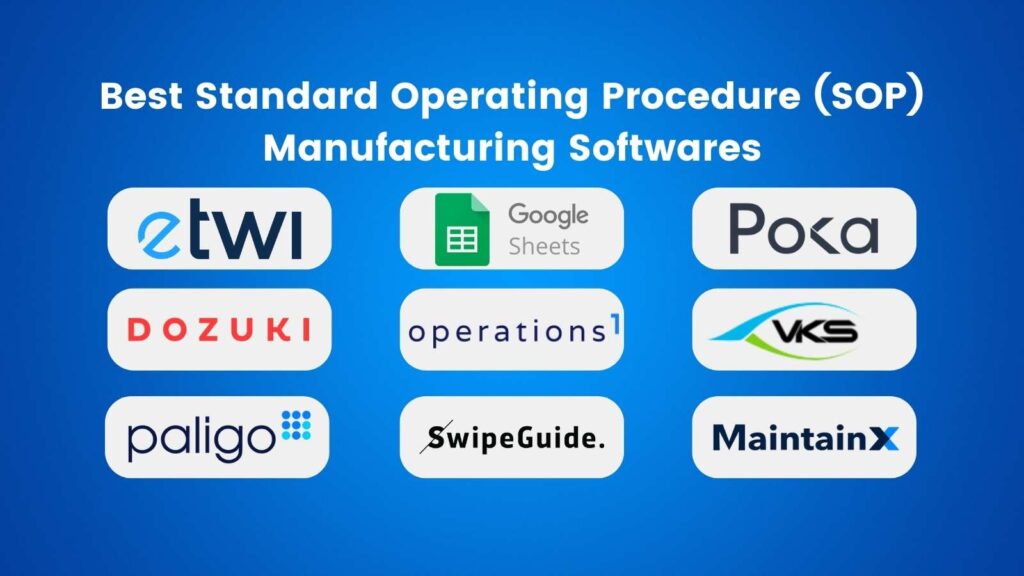
SOP Software – Ranking
Implementing SOPs in TPM Activities
The development and implementation of SOPs within the framework of TPM require a systematic approach. Here’s how organizations can standardize TPM activities through SOPs:
- Identify Critical Processes: Begin by identifying key processes that significantly impact equipment reliability, production efficiency, and product quality.
- Develop SOPs: For each identified process, develop an SOP that outlines the step-by-step tasks required to perform the process effectively and safely. These SOPs should be developed collaboratively with input from operators, maintenance personnel, and engineers to ensure they are practical and comprehensive.
- Training and Education: Ensure that all relevant personnel are trained on the SOPs. Training should be hands-on, allowing employees to become familiar with the procedures and understand the rationale behind them.
- Implementation and Monitoring: Implement the SOPs and monitor their adherence and effectiveness. Regular audits and inspections can help ensure that the procedures are followed and identify areas for improvement.
- Continuous Improvement: Use feedback from the implementation phase to refine and improve the SOPs. Encourage employees to suggest improvements and incorporate their feedback into revised versions of the SOPs.
- Documentation and Accessibility: Maintain up-to-date documentation of all SOPs and ensure they are easily accessible to all relevant personnel. Digital platforms can be used to facilitate access and updates.
Training in TPM with Training Within Industry (TWI)
Training is a cornerstone of Total Productive Maintenance (TPM) because it equips employees with the knowledge and skills necessary to maintain equipment effectively, identify opportunities for improvement, and contribute to the overall efficiency and quality of the production process. An effective methodology that complements TPM in this regard is Training Within Industry (TWI). Developed during World War II to support the rapid training of workers in various industries, TWI has proven to be a valuable framework for implementing structured training programs within the context of TPM.
TWI’s Role in TPM
TWI consists of three core programs: Job Instruction (JI), Job Methods (JM), and Job Relations (JR), each addressing different aspects of job training and improvement. These programs align closely with the goals of TPM, particularly in fostering a culture of continuous improvement, empowering employees to take responsibility for their machinery, and enhancing the overall productivity and safety of the workplace.
Job Instruction (JI)
Job Instruction focuses on teaching supervisors and team leaders how to train employees quickly and effectively. The JI method is particularly relevant to TPM’s autonomous maintenance pillar, as it ensures that operators are proficient in the basic maintenance tasks required for their equipment. The JI four-step method consists of:
- Prepare the Worker: Put the learner at ease, explain the job’s importance, and establish the intent to teach the job.
- Present the Operation: Demonstrate the task, breaking it down into manageable steps while clearly explaining each key point and the reasons behind them.
- Try Out Performance: Have the learner perform the task, correct mistakes, and reiterate the key points.
- Follow Up: Put the learner on their own, gradually reduce supervision, and encourage questions to ensure continuous learning.
Job Methods (JM)
Job Methods training is designed to teach supervisors and employees how to improve the way jobs are done. This aligns with TPM’s focused improvement pillar by encouraging workers to identify and eliminate waste in processes, increase productivity, and improve the use of resources. JM emphasizes breaking down jobs into their constituent steps and critically analyzing each step to find improvements. The JM four-step process includes:
- Break Down the Job: List all job steps as currently performed.
- Question Every Detail: Critically examine each step to identify improvements.
- Develop the New Method: Reconstruct the job steps incorporating the identified improvements, while ensuring safety and quality.
- Apply the New Method: Implement the improved method, train employees in it, and continue to refine the process over time.
Job Relations (JR)
Job Relations focuses on building positive relationships between supervisors and employees, which is crucial for the successful implementation of TPM. A positive work environment encourages teamwork, facilitates communication, and ensures that employees are motivated to participate in maintenance activities. The JR method teaches supervisors how to handle problems, prevent them, and earn the cooperation and respect of their team through four main principles:
- Develop and Maintain Good Relations: Treat team members as individuals, respect their contributions, and be genuinely interested in their welfare.
- Let Each Worker Know Their Job: Clearly communicate job details, expectations, and the importance of their role in the success of TPM.
- Give Credit When Due: Recognize and acknowledge contributions and improvements made by employees.
- Tell People in Advance About Changes: Inform team members about changes that will affect them, explain the reasons, and involve them in the transition process.
Implementing TWI within TPM
To integrate TWI into TPM, organizations should:
- Assess Training Needs: Identify skill gaps related to maintenance tasks, safety procedures, and improvement processes.
- Customize TWI Programs: Adapt TWI’s core programs to the specific needs and context of the organization’s TPM goals.
- Train the Trainers: Develop a group of internal TWI trainers who can effectively deliver the JI, JM, and JR programs to their peers.
- Monitor and Evaluate: Regularly assess the effectiveness of the TWI training programs in achieving TPM objectives, and adjust the training as needed.
Incorporating TWI into TPM enhances the effectiveness of training programs, ensures that all employees are skilled in maintaining and improving equipment and processes, and fosters a culture of continuous improvement and collaboration. This chapter underscores the critical role of training within TPM and provides a framework for integrating TWI to achieve manufacturing excellence.
Constructing a TPM Schedule
Creating a Total Productive Maintenance (TPM) schedule is a pivotal step in ensuring the successful implementation and sustainability of TPM practices within an organization. A well-structured TPM schedule not only delineates the timing and frequency of maintenance tasks but also integrates training, continuous improvement activities, and performance monitoring. This chapter outlines the essential components of a TPM schedule and guides how to build an effective schedule using an active approach.
Essential Components of a Schedule
A comprehensive TPM schedule should include the following components:
- Preventive Maintenance Tasks: Schedule regular and systematic inspections, cleaning, lubrication, and adjustments to prevent equipment failures.
- Predictive Maintenance Activities: Incorporate condition-based maintenance tasks, such as vibration analysis, thermography, and oil analysis, to predict equipment failures before they occur.
- Corrective Maintenance Work: Plan for the timely correction of identified issues during preventive and predictive maintenance to restore equipment to its optimal operating condition.
- Autonomous Maintenance Activities: Allocate specific times for operators to conduct routine cleaning, inspection, and minor maintenance tasks, enhancing their ownership and understanding of their equipment.
- Focused Improvement Projects: Schedule regular meetings and work sessions for cross-functional teams to work on continuous improvement projects aimed at eliminating losses and improving efficiency.
- Training and Education: Include dedicated time slots for training employees in TPM principles, maintenance skills, and the use of new tools and technologies.
- Safety Inspections and Activities: Integrate safety checks and related activities to ensure a safe working environment and compliance with regulations.
- Review and Planning Meetings: Plan periodic review meetings to assess the progress of TPM activities, discuss challenges, and adjust the schedule as necessary.
Building an Effective TPM Schedule
Begin by assessing the criticality of each piece of equipment to prioritize maintenance activities based on their impact on production and quality. This assessment helps focus resources on the most important equipment, ensuring reliability and performance. For each critical piece of equipment, develop a detailed maintenance plan that outlines preventive, predictive, and corrective maintenance tasks, along with their frequency. This plan should be based on the manufacturer’s recommendations, historical maintenance data, and the equipment’s performance.
Incorporate Autonomous Maintenance
Engage operators in the scheduling process by allocating specific times for autonomous maintenance activities. Ensure that these activities are balanced with production demands and that operators are trained to perform them effectively.
Schedule Continuous Improvement Activities
Identify regular time slots for focused improvement activities. Encourage cross-functional teams to use this time to analyze equipment performance, identify inefficiencies, and implement solutions.
Plan for Training and Education
Dedicate time for ongoing training and education, ensuring that all employees have the opportunity to enhance their skills and knowledge in maintenance practices, TPM principles, and safety protocols.
Ensure Flexibility
While it’s important to adhere to the schedule, maintain flexibility to accommodate unexpected maintenance needs, production changes, and opportunities for improvement. Regularly review and adjust the schedule to reflect these changes and learnings.
Communicate and Collaborate
Effectively communicate the TPM schedule to all stakeholders, ensuring that everyone understands their roles and responsibilities. Foster a collaborative environment where feedback is encouraged and used to refine the schedule.
Monitor and Adjust
Regularly monitor the execution of the TPM schedule and its impact on equipment performance and production efficiency. Use key performance indicators (KPIs) to measure success and identify areas for adjustment.
By following these guidelines, organizations can construct a TPM schedule that not only ensures the reliability and efficiency of their equipment but also fosters a culture of continuous improvement and employee empowerment. An effective TPM schedule is dynamic, adjusting to the evolving needs of the organization and its equipment, and is a critical tool in achieving operational excellence.
Conclusions
Total Productive Maintenance (TPM) represents a comprehensive and proactive approach to maintenance management, emphasizing the importance of involvement from all levels of an organization. Through its implementation, TPM aims to achieve zero breakdowns, zero defects, and zero accidents, thereby enhancing the overall efficiency and productivity of manufacturing operations. The chapters outlined in this guide provide a foundational understanding of TPM, focusing on key aspects such as standardization, training, and scheduling, which are crucial for the successful deployment of TPM practices.
Key Takeaways
- Standardization: The development and implementation of standard operating procedures (SOPs) within TPM activities ensure consistency, reduce variability, and improve efficiency across all maintenance and production tasks. Standardization serves as the backbone of TPM by providing a clear and structured framework for all processes.
- Training Within Industry (TWI): TWI plays a significant role in TPM by enhancing the skills and knowledge of employees. By integrating TWI’s Job Instruction, Job Methods, and Job Relations programs, organizations can ensure that their workforce is well-equipped to contribute to TPM objectives, fostering a culture of continuous improvement and collaboration.
- TPM Schedule: Constructing an effective TPM schedule is essential for coordinating maintenance activities, training, continuous improvement projects, and safety initiatives. A well-planned schedule ensures that resources are allocated efficiently, maintenance tasks are performed proactively, and opportunities for improvement are systematically pursued.
Operational Excellence
Implementing TPM requires a strategic and integrated approach, involving:
- Commitment from Top Management: Successful TPM implementation starts with strong leadership and commitment from top management, ensuring that TPM becomes a core part of the organizational culture.
- Employee Empowerment: Empowering employees at all levels to take ownership of their equipment and processes is crucial. This involves providing them with the necessary training, resources, and authority to make decisions and implement changes.
- Continuous Improvement: TPM is an ongoing journey, not a one-time project. Organizations must foster a culture of continuous improvement, where feedback is actively sought, and processes are regularly reviewed and optimized.
- Cross-Functional Collaboration: Effective TPM implementation requires collaboration across different departments and functions. This collaborative approach ensures that maintenance strategies are aligned with production goals and that improvements are holistic and sustainable.
Final Thoughts
TPM is more than just a maintenance strategy; it is a comprehensive approach that seeks to maximize the effectiveness of production equipment, improve product quality, and ensure a safe working environment. By focusing on standardization, training, and scheduling, organizations can lay a solid foundation for their TPM initiatives, leading to significant improvements in operational performance and competitiveness. As industries continue to evolve, the principles of TPM remain relevant, providing a framework for organizations to adapt to changes, overcome challenges, and achieve excellence in their operations.